With Quick-EtherCAT, real-time Industry 4.0 applications can be updated quickly because it uses graphical programming tools and Big Data databases.
With Quick-EtherCAT to the Smart Factory: Modern manufacturing technology for Industry 4.0
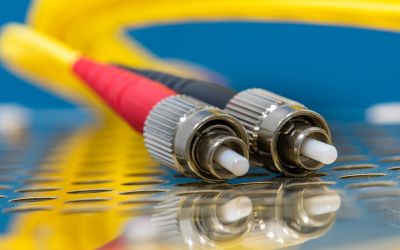
Automation and networking: The future of manufacturing in Industry 4.0 (Foto: AdobeStock – salita2010 331275724)
In manufacturing, intelligent automation has taken hold on a global scale. Companies are forced to face the challenges of Industry 4.0 in order to remain competitive. The shortage of skilled workers is another challenge, forcing companies to find new methods to increase productivity and reduce operating costs. Process automation plays an important role in this by writing programmes to optimise the manufacturing process and reduce errors.
QEC offers a wide range of EtherCAT modules that can be used in industrial applications. The company specialises in the development of hardware and software specifically tailored to the requirements of EtherCAT. QEC’s EtherCAT Master and EtherCAT Slave modules provide a reliable and efficient solution for real-time communication in industry and contribute to more economical IoT technology.
To accelerate the implementation of Industry 4.0 in the manufacturing industry, ICOP has developed a complete EtherCAT solution based on the Arduino platform. The solution offers comprehensive and user-friendly programming with graphical tools and a powerful SQL database to store and analyse the collected data. The EtherCAT solution enables efficient data communication between different machines and sensors, facilitating the implementation of Industry 4.0 concepts.
“EtherCAT: High-performance communication for industrial applications”
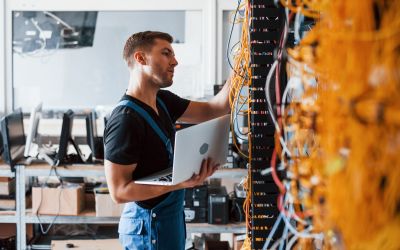
EtherCAT from Beckhoff offers efficient on-the-fly communication thanks to full duplex and low overhead. (Foto: AdobeStock – standret 302670228)
The real-time Ethernet technology EtherCAT was developed by Beckhoff and is supported by the EtherCAT Technology Group. The protocol is based on the IEC 61158 standard and is particularly suitable for applications in automation technology, test and measurement technology and many other areas. EtherCAT is characterised by particularly fast and efficient communication, as each device is read and written in real time. The daisy-chain topology enables simple and flexible integration of devices and systems. Due to its high flexibility and scalability, EtherCAT is also suitable for demanding applications in Industry 4.0.
Distributed Clocks for High-Precision Synchronisation is another important feature of EtherCAT. With this feature, devices and machines can be precisely synchronised to ensure smooth cooperation. By using Distributed Clocks, the latency between devices can be minimised, resulting in higher accuracy and reliability.
EtherCAT is a fieldbus technology that enables all participating slaves in a network to communicate synchronously and exchange their data. The addressing mode of EtherCAT enables fast and efficient transmission of data via the fieldbus by integrating all slaves into the transmission protocol. The memory control technology “Fieldbus Memory Management Unit (FMMU)” ensures that the data transmission takes place smoothly and without errors.
ICOP Technology will present ist entire product range of EtherCAT master and slave products at Embedded World 2023 in Nuremberg. All devices rely on the proven FMMU technology, which enables a fast data exchange of up to 1000 data units within only 30 µs. With this technology, users can realise real-time applications in Industry 4.0 and make their production processes even more efficient.