The battery has become increasingly popular as one of the most accessible energy storage solutions in recent years. It is now widely used not only in consumer electronics, mobile tools, and uninterruptible power supply systems (UPS), but also in electric vehicles and renewable energy storage. However, the different characteristics of various battery types present challenges for consumers and engineers when it comes to selecting batteries and chargers. This article will discuss the differences between two of the most common types, lead-acid and lithium batteries, as well as the selection of a suitable charger.
Table of Contents: What awaits you in this article
Advantages and disadvantages of lead-acid batteries for energy storage
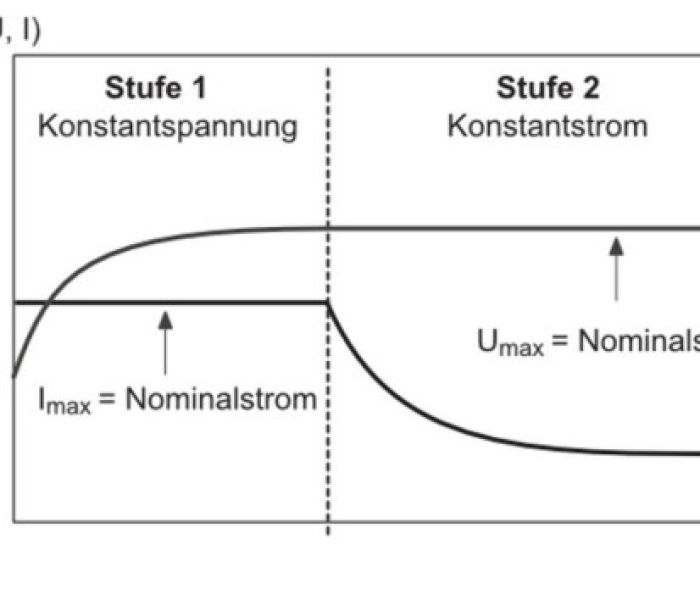
Abb. 2: 2-Stufenladung (Foto: FORTEC Power GmbH)
Blei-Säure-Akkus sind aufgrund ihrer zahlreichen Vorteile und ihrer langen Geschichte als einer der beliebtesten Akkutypen bekannt. Sie zeichnen sich durch eine hohe Toleranz bei der Ladespannung, eine hohe Stoßstromfähigkeit und einen breiten Betriebstemperaturbereich aus. Zudem sind sie im Vergleich zu anderen Akkus recht preiswert. Aus diesen Gründen werden sie oft als Starterbatterien in Kraftfahrzeugen, für den Antrieb von Gabelstaplern und in Notstromsystemen eingesetzt. Allerdings haben Blei-Säure-Akkus auch einige Nachteile wie eine hohe Selbstentladungsrate, ein hohes Gewicht und eine begrenzte Zyklenlebensdauer, weshalb sie für Energiespeicheranwendungen nur begrenzt geeignet sind.
Lithium batteries are known for their superior cycle life, meaning they can be charged and discharged more times before losing capacity. With a cycle life of approximately 1000-3000 cycles, they are perfect for long-term energy storage. Depending on the cathode material, there are different types of lithium batteries with varying performance. Lithium Cobalt Oxide (LCO) offers high energy density and is commonly used in consumer electronics. Lithium Iron Phosphate (LiFePO4), on the other hand, has a longer lifespan and better thermal stability, making it a preferred choice for energy storage solutions. However, it is important to note that lithium batteries can be prone to overheating and may pose a fire hazard if not properly monitored during charging and discharging.
Understanding the Voltage Range and Capacity of Lead-Acid Batteries
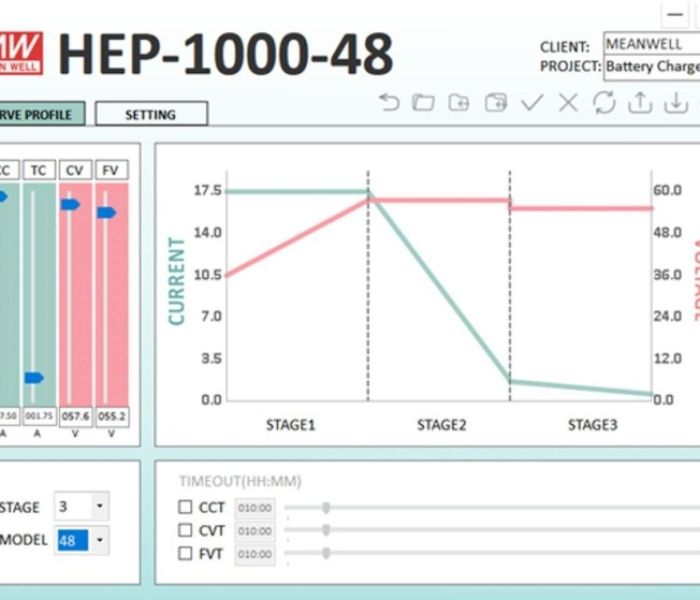
Abb. 3: Programmieroberfläche, HEP-1000-48, 3-Stufenladung (Foto: FORTEC Power GmbH)
The nominal voltage of a single lead-acid cell is approximately 1.8 – 2.3 V DC. Typically, they can be charged with a C coefficient ranging from 0.1C to 0.3C. Commercially available batteries often consist of multiple cells connected in series and parallel to form a high-capacity battery with commonly used output voltages such as 12, 24, and 48 V DC. The labels “12V,” “24V,” or “48V” on the battery are merely indications of the voltage range. The actual voltage constantly changes depending on the remaining capacity. For example, the open circuit voltage of a typical 12V lead-acid battery can range from 10.8V (30% battery capacity) to 13.8V (100% capacity).
Understanding the C-Coefficient: A Key Factor in Battery Charging
The C-coefficient, also known as C-factor or C-rate, is a measure of the relative charge or discharge current compared to the battery’s capacity. It is calculated by dividing the maximum allowable charge or discharge current by the battery’s capacity. A C-coefficient of 1C means that the battery can be fully charged or discharged within one hour. For example, a C-coefficient of 0.3C indicates that the battery can be charged in approximately 3 hours and 20 minutes.
The 3-stage charging method is often recommended for lead-acid batteries due to their high self-discharge rate. The charging cycle begins with a constant current charging phase, where the charger limits its output current to the maximum rated value and gradually increases its output voltage. Once the battery voltage reaches the maximum charging voltage, the charger switches to a constant voltage phase.
The charger gradually increases its output voltage to reach the maximum rated voltage while monitoring the output current. Once the battery reaches its maximum charge, the charger switches to a maintenance charge mode, where the output current drops to about 10% of the rated current. During this phase, the charger reduces its output voltage to prevent overcharging. Even though the battery is almost fully charged at this point, it continues to draw a small amount of current from the charger to compensate for self-discharge.
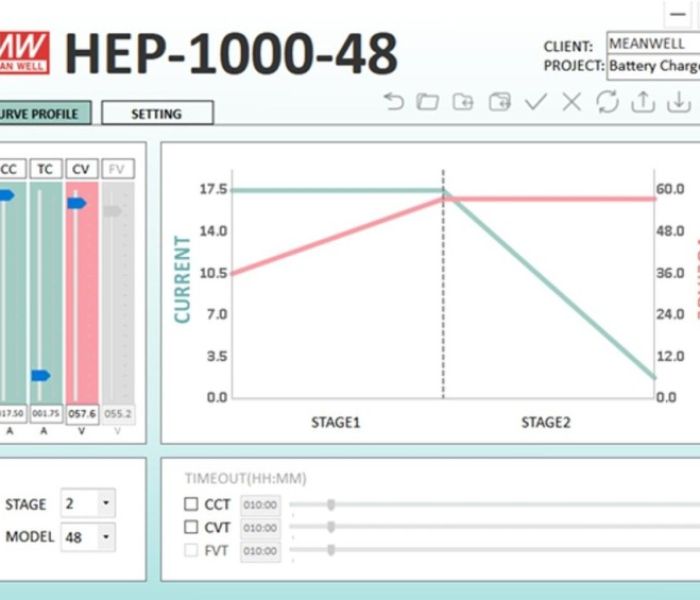
Abb. 4: Programmieroberfläche, HEP-1000-48, 2-Stufenladung (Foto: FORTEC Power GmbH)
Lithium batteries have a voltage range of 3.2V to 4.4V and can be charged at a maximum C-rate of 1C. It is important to note that even lithium batteries with the same materials may have different nominal voltages and charge currents, especially if they are manufactured by different companies. Unlike lead-acid batteries, lithium batteries cannot tolerate high charging voltages and do not require maintenance charging to maintain their state of charge. Therefore, a two-stage charging process without the maintenance stage is commonly used for charging lithium batteries.
Due to the varying manufacturing tolerance of cells in large lithium battery banks, the equivalent series resistance (ESR) of lithium cells cannot be perfectly matched. This leads to cells in the same bank being charged or discharged with different voltages or currents. Cells with low ESR are always fully charged or discharged first, causing them to age and fail faster than other cells in the bank.
The imbalance between cells not only reduces the battery’s lifespan but also poses a significant safety risk by potentially causing thermal runaway. To address this issue, large lithium battery banks should always be equipped with Battery Management Systems (BMS). The primary function of a BMS is to monitor the charging state and balance the cells either passively or actively.
A passive battery management system (BMS) equalizes the charge levels of individual cells by discharging the fuller cells using power resistors. While a passive BMS is relatively simple to construct, it is not as efficient or effective. In contrast, an active BMS charges the cells individually to balance their charge levels. With the active BMS taking control of the charging process for each cell, some lithium battery banks with active balancing BMS only require constant voltage AC/DC power supplies as chargers.
Optimizing Battery Charging Curves for Reliability, Longevity, and Safety
Different types of batteries from various manufacturers can have varying characteristics. To ensure reliability, longevity, and safety, it is recommended (and mandatory for lithium batteries) to optimize the charging curve for each battery. MEAN WELL’s programmable chargers, such as the NPB-450/750/1200/1700, RPB-1600, RCB-1600, DBU-3200, DBR-3200, DRS-240/480, HEP-2300-55, and HEP-1000, along with the SBP-001 intelligent programming device, provide high flexibility and a user-friendly interface for customizing the charging curve.
The HEP-1000-48 is a reliable constant voltage power supply with a standard configuration of 48 V DC and a maximum power of 1008 W. It can be reprogrammed into an intelligent charger using the MEAN WELL Smart Charger programming device SBP-001. The default charging curve for typical lead-acid batteries is a 3-stage curve (refer to Figure 3), with a boost charging voltage of 57.6 V DC and a floating charging voltage of 55.2 V DC. The charging voltage and current can be adjusted from 36 to 60 V DC and from 3.5 to 17.5 A respectively for different types of lead-acid batteries.
By adjusting the programming interface, the 3-stage charging of the HEP-1000-48 can be modified to a 2-stage charging, allowing it to be used for charging lithium batteries. For example, when charging a 20 Ah LiFePO4 battery with a maximum charging voltage of 56 V DC, the “CV” and “CC” options shown in Figure 4 can be set to 56 V DC and 17.5 A to achieve the fastest charging. The user can also lower the charging current to avoid excessive temperature rise caused by high currents. Additionally, the charging voltage can be lowered to prevent overcharging of the battery.
MEAN WELL programmable chargers optimize battery charging for longer lifespan
The programmable chargers from MEAN WELL provide the capability to customize charging curves, which are necessary for optimal charging of lead-acid or lithium batteries. By optimizing the charging voltage and current, the chargers protect the batteries, utilize their available capacity, and extend their lifespan.